在PCB设计中,导通孔(Via)是实现多层电路互连的关键结构。根据其贯穿范围和制造工艺,导孔主要分为通孔(Through Via)、盲孔(Blind Via)和埋孔(Buried Via)三种类型。本文将系统解析它们的技术特征与应用场景。
一、通孔(Through Via)
定义: 贯穿PCB所有层的导通孔,从顶层直达底层。这是最传统且广泛应用的导孔类型,在四层板中即贯穿1-2-3-4层。
制造工艺: 通常采用机械钻孔,孔径≥0.2mm;高密度板使用激光钻孔,孔径可达0.1mm。需进行电镀处理形成导电通路,支持插件元件安装与层间信号传输。
|
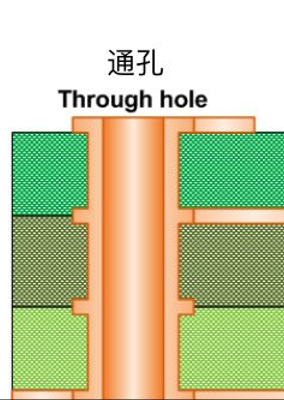 |
特点与应用:
· 优点:工艺成熟、成本低,适合大电流/机械固定需求(如螺丝孔);
· 缺点:占用垂直空间,影响布线密度,高速信号可能因过长走线引发干扰;
· 典型应用:通用电路板、功率器件安装区域。
设计要点: 孔径需满足电气(载流能力)与机械(焊盘尺寸)要求,阻焊层处理需防止锡珠污染。
|
二、盲孔(Blind Via)
定义: 仅连接表层与内层的非穿透孔,通常从顶层至第2层或底层至倒数第2层。例如表面层延伸至内层的短导孔。
制造工艺:
· 激光盲孔:精度达±0.025mm,适用于HDI高密度互连板;
· 机械盲孔:成本较低但深度精度有限(公差±0.05mm)。 需在层压前完成钻孔镀铜,深度控制需考虑材料膨胀系数与镀层均匀性。
|
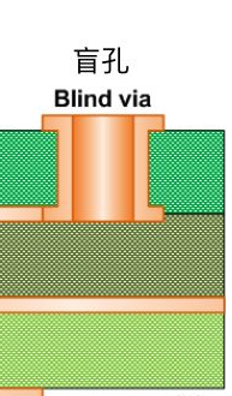 |
特点与应用:
· 优点:节省表层空间,缩短信号路径(减少约30%阻抗),提升高频信号完整性;
· 缺点:钻孔精度要求高(深度≤孔径6倍),不良率影响成本;
· 典型应用:手机主板、射频电路、超薄设备等空间敏感型场景。
设计标准: IPC-6012 Class 3要求盲孔深径比≤1:1,电镀层厚度≥0.8mil(20μm)保证可靠连接。
|
三、埋孔(Buried Via)
定义: 完全隐藏于多层板内部的内层导通孔,连接任意两非表层内层(如L2-L5),外部不可见。
制造工艺: 采用分层压合技术:先局部层压+钻孔镀铜,最终整合为完整板体。需多次精密对位(对位偏差≤15μm)。
|
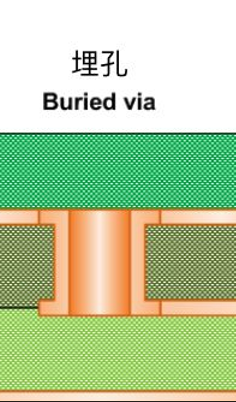 |
特点与应用:
· 优点:最大限度释放表面空间,实现超精细布线(线宽/间距达3/3μm),消除通孔阴影效应;
· 缺点:工艺复杂度极高(成本增加40%以上),返修几乎不可行;
· 典型应用:大型CPU基板、光模块、汽车雷达PCB等高密度多层板。
制造难点: 内层孔径公差需控制在±10%,钻孔后需进行等离子清洗防止残胶影响镀层附着力。
|
四、对比总结与选择指南
类型
|
贯穿性
|
工艺复杂度
|
成本
|
适用场景
|
通孔
|
全层穿透
|
低
|
低
|
传统电路、电源/地信号
|
盲孔
|
单侧穿透
|
中
|
中高
|
HDI板、高频高速设计
|
埋孔
|
内层互联
|
高
|
极高
|
超高密度板、特殊领域
|
关键选择因素:
1. 密度需求:盲孔适合表层优化,埋孔针对内层扩展
2. 信号完整性:高速电路优先埋孔/盲孔(信号延迟降低15%-25%)
3. 成本控制:通孔占比≥80%为经济方案
五、前沿趋势
· 超微孔技术:激光开孔直径突破75μm,5G基站PCB中实现10:1深径比
· 电镀工艺革新:垂直连续电镀(VCP)缩短镀铜流程30%
· 材料改进:低介电常数层压板(Dk<3.0)拓宽埋孔应用上限
随着电子产品向小型化、多功能化演进,盲孔与埋孔的工艺成熟度持续提升,设计者需综合评估性能、周期与成本,制定最佳导孔设计方案。